Motivation
The industrial product to be simulated and subsequently optimised is a Professional Desktop 3D Printer with two printing heads based on Fused Filament Fabrication (FFF) Technology. This technology is shifting from desktop specialized users to more industrial applications; which require improved quality, throughput and minimum human intervention.
In order to answer to this demand, the project will develop a Digital Twin (DT) of the process which is coupled to the machine controller thanks to the continuous monitoring of filament feed in order to bring auto stabilizing capabilities to the process and enable improved reliability for long printing jobs that last days; thus avoiding painful process failures. The strategy of BCN3D is to be distinguished for selling machines that produce good 3D printed parts relying into a deep and continuously updated knowledge of the extrusion process, for different materials (including polymers, reinforced plastics, and metal filaments).
Preliminary experiments by BCN3D have shown that process instability can be anticipated based on the monitoring and process measurement. DIGITbrain has been identified as an opportunity to further include an IoT concept to the new electronics, before unexplored. The final aim is to develop a very sensitive self-adjustment capability so that any process drift can be monitored and bring it to stability, thus facilitating MaaS production models and increase confidence in this production method.
Purpose of the Experiment
The aim is to demonstrate the feasibility of controlling the extrusion process (MODEL), “keep it healthy” during the continuous printing of large jobs (days) with a real time and highly sensitive multi level DT control. The experiment seeks to explore the added benefits of the DIGITbrain conceptual approach.
- The experiment will demonstrate for selected geometries and materials that are known to produce problems or under arbitrary disturbances that the DIGITbrain Experiment approach is able to produce improved quality.
- Demonstrate automatic process parameters tunning capability for new materials and enable optimisation based on quality parameters like (productivity, aesthetics, quality/strength).
- The new solution should be able to classify the detected process difficulties or defects based on the available data and corresponding algorithm (clustering,…) and link to 3D geometry or topology.
The process will be stored, paired with the XYZ coordinates so that it will be possible to build a cloud of points data for later quality inspection, and also allocated in the DIGITALbrain repository for process stability and 3D-geometry linking Algorithms development.
The experiment will be devoted to demonstrate the applicability of the approach for the following Life cycle phases:
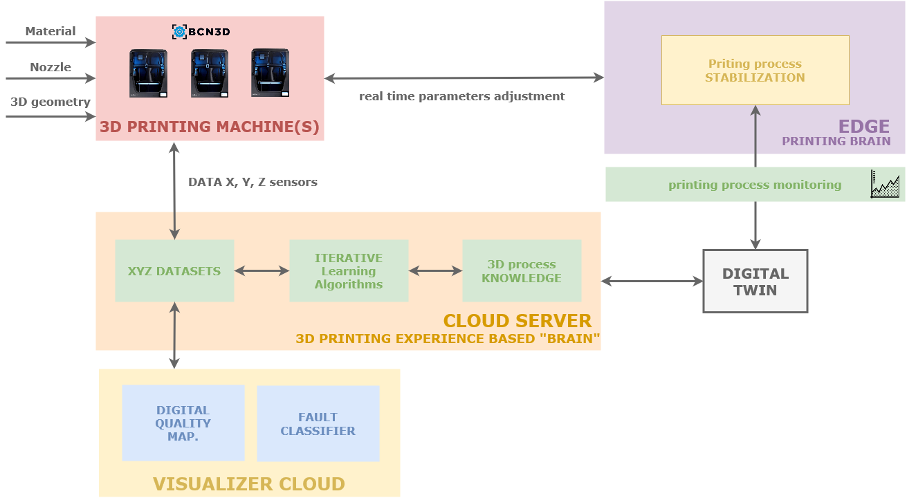
a) Engineering,
b) Quality Assurance,
c) Production/Process Reliability,
d) Maintenance.
The main contribution of 3D-Brain is the combined usage of in a single machine control (edge) and the iterative learning across machines (cloud) across the world wide installed BCN3D machines base.
Technical Impact
The Experiment will bring automatic process tuning capabilities which will be a standard in the near future for Professional 3D Printers; extending the application of the technology and widening the number of end users and technology applications.
The building blocks of the solution, can be summarized as follows.
- Auto Process control, Model: To autotune the printing process variables to keep it stable.
- Quality check Visualization Tool: To analyse a produced part and asses digitally part quality.
- Industrial Product diagnosis Tool: To measure machine hardware and software health based on data analysis. Real time, machine state diagnosis from sensor, and to be extended after the present project with temperature and motor energy consumption.
In the lowest layer, the proposed Cyber-Physical Production Systems for 3D printing will communicate with attached networked devices integrated in the cloud/edge (SAVVY BOX) for continuous data gathering and remote administration, comprising IoT-enabled 3D printing solutions; The printers will additionally be equipped with extended sensing, actuating, and controlling capabilities.
These new functionalities will rely on Physics-based models and data. Computing capacity and data persistency (specially for time-series) will be leveraged from DigitBrain Platform.
In addition to being able to check the 3D printer data, the end user will be able to access the solutions and applications developed in the project via a front-end application.
Expected Economic Impact
The following benefits are intended for the end user(s) of FFF Technology including BCN3D customers
Process / tool / solution innovation: The new functionality will bring auto calibration of optimised parameters. This will bring advanced users and new material researcher the ability to try new materials and auto-tune the process parameters.
The future idea is that the machine users , manage the production in 3D Printing Farms and BCN3D can bring a MAAS Service, assuring process stability and perfect Printing Process.
Cost savings: Users will benefit from reduced scrap and non-productive machine hours as well as avoidance of material parameter experiments. At the same time, the information gathered from the monitoring and the “control” dynamics will allow to detect any incorrect setting of the machine remotely from BCN3D, enabling to a kind of Machine hour renting model in the future or MAAS.
Time reduction : At the same time, the introduction of the process stabilization strategy will allow to use more ambitious printing parameters , contrary to the presently used more conservative sets; due to the ability to process control, thus reducing production time. For more repetitive productions, the machine will gain process knowledge and apply feedforward parameters setting to avoid a priori process instabilities.
Augmented market visibility: By participating and showcasing positive experiment results in a rich digital ecosystem - the DIGITBrain platform and Digital Agora -, exposure users to various industry segments will be elevated and the likelihood of generating interest / attracting key market players increased.
The process improvement and reliability is a natural output of the proposed project and it will bring quality improvements by assuring process control for different materials and 3D geometries.
Project Video of §D_Brain Experiment
Project Partners:
Barcelona Three Dimensional Printers Sl
is an Industrial Product Manufacturer specialized in 3D printing Professional Desktop machines and Manufacturing End-user requirements specialist.
Savvy Data Systems S.L.
is an Independent Software Vendor and a provider of cloud-based, Data and IoT solutions.
Ideko S. Coop.
is a Spanish Research Centre, specialized in Manufacturing and Production Technologies.
ITAINNOVA
is the Digital Innovation Hub with the role of experiment supervisor.